Sign up to the CM newsletter for free, delivered direct to your inbox.
The UK’s Most-Read Construction Magazine. Prefabricated Metal Sheds
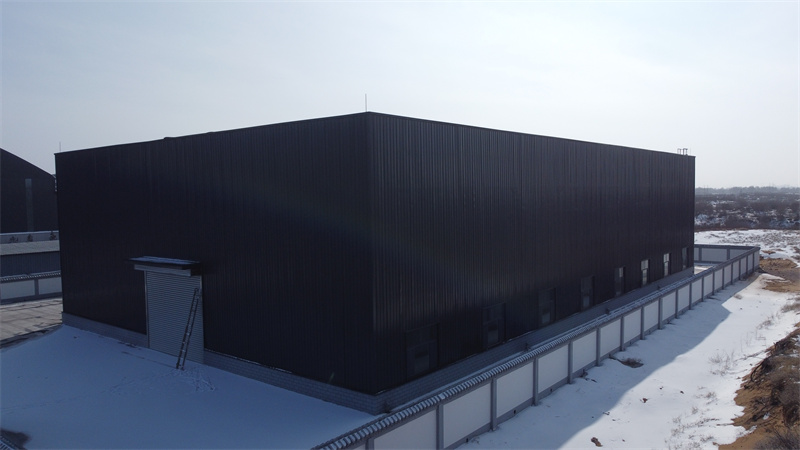
Construction Management is the highest circulation construction-based publication serving the UK built environment.
Marks & Spencer wanted to tear down its steel-framed Oxford Street store. But these buildings can be repurposed, rather than demolished, in favour of new-build, and steel-framed structures provide many examples of how this is possible, writes Martin Cooper.
Michael Gove’s rejection of Marks & Spencer’s application to redevelop its flagship Oxford Street site highlighted the growing concern about new-build proposals involving demolition of existing structures.
The secretary of state for the Department for Levelling Up, Housing and Communities said the plan did not “support the transition to a low-carbon future and would overall fail to encourage the reuse of existing resources, including the conversion of existing buildings”.
But while Marks & Spencer wanted to tear down the steel-framed retail store, elsewhere in London, the trend of retrofitting and refurbishing existing buildings is on the rise. According to Deloitte’s bi-annual London Office Crane Survey, 37 refurb schemes covering 297,000 sq m began on site in the six months to March 2023 – the highest number and volume since Deloitte began tracking in 2005.
And steel has proven to be ideal framing material for redevelopment projects, notably in the office sector. Where developers are looking to add valuable extra floors, the material’s lightweight attributes make it suitable for both existing concrete and steel-framed buildings.
Quite often, the addition of new steel-framed floors can be achieved with minimal strengthening of the structure’s original foundations and superstructure, creating a cost-effective and sustainable construction solution.
An example of steel construction offering the solution for an extensive office redevelopment is British Land’s 1 Triton Square, originally built for the First National Bank of Chicago and opened in 1997. This concrete-framed office building was the first structure to be completed at Regent’s Place, a 5.2 ha mixed-use campus on the north side of London’s Euston Road.
The original five-storey building’s large central atrium was partially infilled with steelwork, increasing the office floorplates, while three new floors were added to the top of the structure, adding even more valuable commercial space. Overall, steelwork contractor William Hare installed 2,142t of new steelwork for the project.
Lendlease project director Chris Carragher says the decision to refurbish the building instead of demolishing it was all about creating the most sustainable construction solution possible and is testament to British Land’s sustainable values.
“Refurbishing a project is a more environmentally-friendly option, as well as being cost-effective,” he says.
“35,000t of concrete and 1,900t of steel were re-used and saved from demolition.”
Further highlighting the benefits of the chosen construction method, compared to a typical commercial building job, cost savings of 43% were made, while overall it was 30% quicker to complete.
According to Arup structural lead Andrew Robertson, there were also significant carbon savings for this refurbishment compared with a new build equivalent.
“About 35,000t of concrete and 1,900t of steel were re-used and saved from demolition. The re-use of the structure and facade elements resulted in carbon savings equivalent to a gas and electricity emission-free operation for 26 years.”
British Land set high sustainability aspirations for 1 Triton Square through its Sustainability Brief for Developments, which sets targets for exemplary wellbeing, community, futureproofing, and skills and opportunities. The project gained a BREEAM ‘Outstanding’ rating and has been named one of the UK’s most sustainable HQs.
A similar design scenario played out at 160 Old Street, London. Here, a former 1970s concrete-framed Post Office administrative building has been redeveloped and enlarged with the aid of steel construction, provided by subcontractor Bourne Steel.
The project team says that the lightweight nature of the steel-framed solutions enabled two floors to be added to one elevation of the building, increasing this side of the structure from six to eight-storeys.
Meanwhile, two floors were also added to the Bunhill Row elevation, increasing this part of the scheme from five to seven floors.
Another steel-framed floor was also added to the Banner Street elevation, while internally, a new four-storey steel-framed element takes up much of the space that was created by demolishing a 1980s-concrete extension.
“Using a lightweight composite solution of structural steelwork supporting metal decking to form new upper floors and a new internal zone meant there was little or no strengthening works necessary to the foundations or existing concrete columns,” explains Heyne Tillett Steel associate director Krzysztof Marcinkiewicz.
Reusing the project’s foundations and much of the original superstructure did not just have sustainability benefits, it also allowed the project to achieve a very quick construction programme.
Steelwork’s aesthetic attributes were also a consideration and benefit to the scheme. The steel beams, columns and services are all exposed throughout the building, creating the modern industrial-style interior many office tenants want these days.
Another British Land project in the capital has demonstrated the advantages of retaining an existing steel-framed structure and then adding new steelwork to increase its gross internal floor area (GIFA).
Forming an initial phase of the City of London’s wider Broadgate redevelopment, 100 Liverpool Street consisted of two existing buildings that have been reconfigured into a single mixed-use structure.
Totalling 66,000 sq m, the project achieves a 40% increase in leasable floor area, while assimilating 50% of the existing superstructure and 100% of the foundations.
New steelwork has knitted the structures together, replacing some demolished areas and adding four new floors to the top, creating a new 10-storey landmark building.
Sustainability was also at the core of this design, as only steel construction would have allowed the project to reuse the foundations, and then strengthen retained steelwork to allow them to support the new lightweight steel-framed floors.
“The project shows the unique circular-economy credentials of steel-framed construction. The steel industry’s fantastic quality-control processes and provenance have enabled the retention of much of the existing frame,” explains AKT II technical director David Watson.
Steelwork’s high strength allowed novel strengthening details to carry the additional loads with minimal new material and waste. The team added floors and reworked the existing steel structure to create an elegant new City office with high sustainability credentials.
For steel-framed buildings, the trend away from demolish and new-build to retain, refurbish and extend shows no signs of slowing, with clear gains from a financial, programme and sustainability perspective. Perhaps the Marks & Spencer flagship store on Oxford Street will be next.
I wonder if timber frame would have been possible for these refurbished projects.? Surely more sustainable than steel…
The February 2024 issue of Construction Management magazine is now available to read in digital format.
NASC Yearbook 2024 is now available to read in digital format.
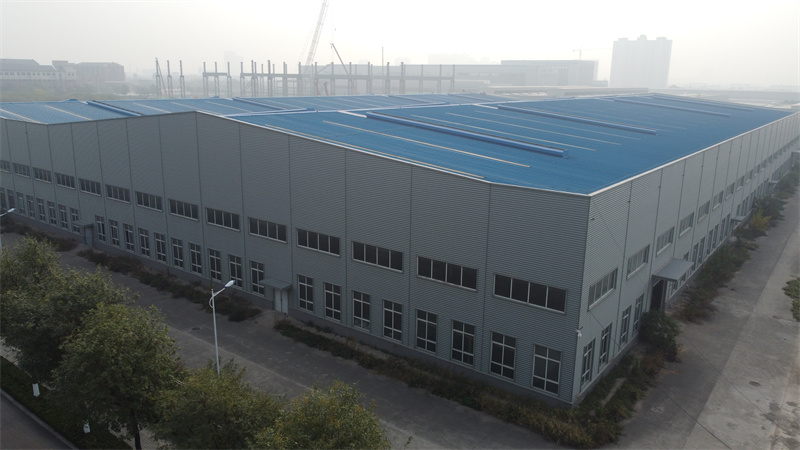
Steel Prefab Building This is not a first step towards a paywall. We need readers to register with us to help sustain creation of quality editorial content on Construction Management. Registering also means you can manage your own CPDs, comments, newsletter sign-ups and privacy settings. Thank you.