Machine tools can produce significant vibration during operation and high levels of machine vibration can adversely affect the enclosed position encoders installed on these machines, leading to measurement inaccuracies. The quality of axis position measurement can directly impact aspects of process quality, such as feature accuracy and surface finish. Position measurement improvements that reduce the influence of vibration can significantly improve the quality of production. The main causes of vibration in machine tools are:
i. Tool chatter, which can occur during the cutting process under certain conditions. For example, when milling hard materials, deflection of either the workpiece or the tool can occur due to excessive cutting forces. Grating Scale Reading Head
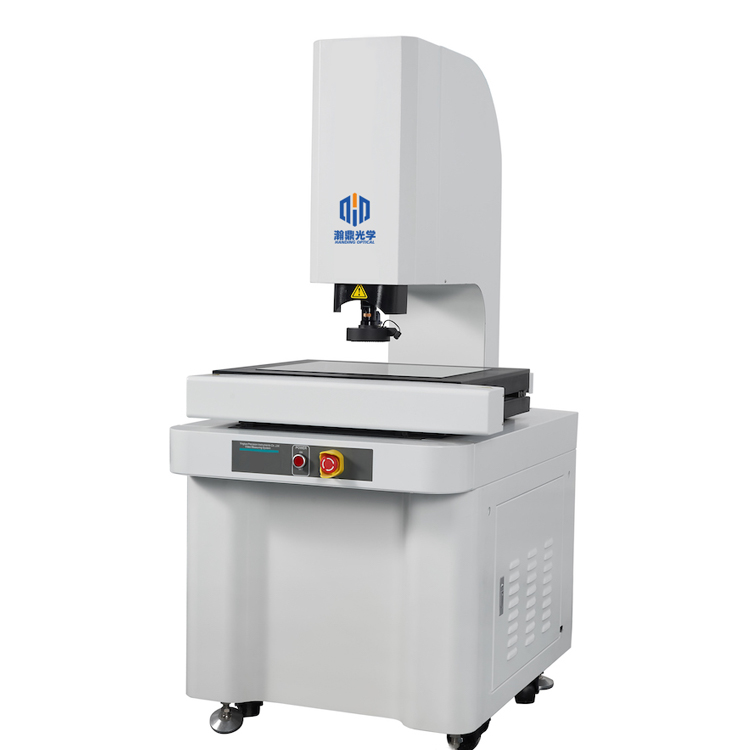
ii: Inhomogeneities in the material being machined and built-up edges on the cutting tools. Due to a sudden increment in machining difficulty, impulsive force is generated which causes vibration.
iii. Intermittent cutting, common in milling, causing impulsive forces to be generated and resulting in vibration.
iv. Disturbances due to unbalanced rotating masses, changes in transmission damping, such as bearing wear, or poor workpiece holding.
v. Worn or poorly maintained machine tools and poor selection of cutting tools, non-optimized spindle speeds and feed rates.
Renishaw’s extensive experience of machine tools has enabled successful partnerships with major machine tool builders as well as end-users. The FORTiS™ enclosed encoder was conceived to address known issues with machine tool vibration and its effects on position measurement. Three features of the FORTiS encoder design combine to improve robustness against mechanical vibration and enhance the encoder’s ability to stop high-amplitude disturbances from entering the position control loop:
1. Conventional enclosed optical encoders feature a sprung, wheeled carriage that supports the readhead body as it runs along the encoder scale, as shown in Figure 2a. At any given driving frequency, the amplitude and phase of vibration of the machine guideway (Vg) supporting the readhead will be different to that of the encoder’s scale and enclosure (Vm), which are fixed on the machine mounting surface; this difference in the amplitude and phase response must be absorbed by the flexures and couplings in the wheeled carriage, as seen in Figure 1. FORTiS encoders employ a contactless design which effectively isolates the readhead body from its enclosure, as shown in Figure 2b.
2. Conventional enclosed optical encoders use a glass scale of relatively high mass, suspended from one side of the enclosure. To avoid unwanted oscillations in the enclosure due to the vibration of the cantilevered scale, the FORTiS encoder uses a light steel scale that is fixed along its full length to the inside of the enclosure body.
3. The third vibration-reducing design feature of the FORTiS encoder is the use of tuned mass damping. A tuned mass damper (TMD) is a mechanical device, mounted to a specific location in a structure, to strongly damp resonant vibration. Two TMDs are used to counteract vibration around the vertical and horizontal axes.
Read the full whitepaper here.
Browse the most current issue of Design World and back issues in an easy to use high quality format. Clip, share and download with the leading design engineering magazine today.
Top global problem solving EE forum covering Microcontrollers, DSP, Networking, Analog and Digital Design, RF, Power Electronics, PCB Routing and much more
The Engineering Exchange is a global educational networking community for engineers. Connect, share, and learn today »

PPG Thickness gauge Copyright © 2024 WTWH Media LLC. All Rights Reserved. The material on this site may not be reproduced, distributed, transmitted, cached or otherwise used, except with the prior written permission of WTWH Media Privacy Policy | Advertising | About Us